Client Overview:
We recently sat down with a cannabis cultivator, manufacturer, and LightLab 3 user who is operating on farmland with extensive water and surface rights. Known for their sophisticated, automated processes, this customer manages a vast operation, producing thousands of cannabis plants annually and processing 300,000 – 400,000 lbs of biomass each year.
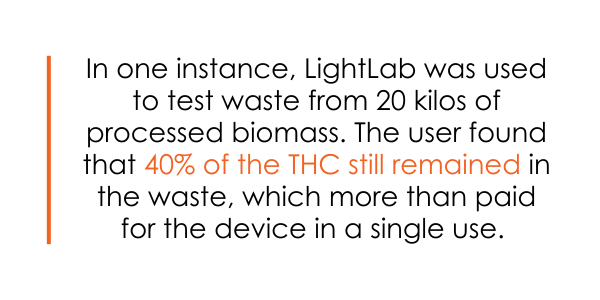
The Challenge: Dialing in Mixed, Large-Scale Manufacturing Equipment
Significant challenges were faced due to the scale and remote nature of their operations:
1. High-Volume, Remote Operations: Managing 1,000 acres and 110,000 plants in a remote location required extensive automation and efficient processes to reduce the need for a large labor force.
2. Complex Processing Needs: The process involved multiple stages, including planting, harvesting, and extracting cannabinoids for distillate and Live Rosin production, each requiring precise control and optimization.
3. Equipment and Process Optimization: With a variety of sophisticated equipment, including combines, conveyors, and membrane filtration systems, the user needed to ensure each piece was finely tuned to maximize efficiency and product quality.
The Solution: Internal Potency Testing with LightLab 3
To address these challenges, the business integrated LightLab 3 Cannabis Analyzer by Orange Photonics into their operations. This portable HPLC potency testing device provided real-time data insights, enabling them to optimize various processes:
1. Ethanol Spraying and Separation: By using LightLab data, the user could determine the optimal settings for their ethanol spray and auger during the distillation process, maximizing cannabinoid extraction and efficiency.
2. Membrane Filtration Efficiency: LightLab allowed the team to monitor and adjust the membrane filtration process, ensuring the highest level of cannabinoid extraction from each batch.
3. Winterization: With LightLab, the team tested winterized product, and the waste fats and waxes, to ensure winterization was complete.
4. Decarboxylation Process: LightLab enabled in-house testing of decarboxylated material, ensuring complete conversion of THCA to THC without the need for external lab testing.
5. Traceability and Data Collection: LightLab facilitates detailed traceability from biomass to final product, helping the user maintain high quality and regulatory compliance.
The Results: Quantitative Improvements and Operational Efficiencies
1. Increased Efficiency and Resource Savings: By optimizing ethanol usage through precise data-informed process adjustments, the user saw significant cost savings. They were able to accurately determine the optimal number of washes per ethanol batch, eliminating guesswork and improving resource management.
2. Enhanced Product Quality: Real-time data from LightLab allowed for continuous monitoring and fine-tuning of processes, resulting in higher-quality distillate and Live Rosin products.
3. Operational Continuity: With the ability to conduct potency testing on-site, the operation of processing up to 1,000 lbs of biomass daily continued without delays related to third-party testing.
4. Rapid ROI: In one instance, LightLab was used to test waste from 20 kilos of processed biomass. The user found that 40% of the THC still remained in the waste, which more than paid for the device in a single use.
5. Empowered Workforce: By simplifying analytical processes, LightLab empowered operators to make data-driven decisions without needing extensive technical expertise. Users don’t need PhDs on staff to run analytical chemistry equipment since they can collect data with LightLab and use that information to empower operators.
Conclusion:
The integration of LightLab 3 by Orange Photonics transformed this LightLab user’s operations, enhancing product quality and moving product through production to retail as rapidly as possible. By leveraging real-time data and optimizing their sophisticated, large-scale equipment, they solidified their position as an industry leader in cannabis cultivation and manufacturing.